Ballot Information
Reference / ISO/DIS 10423 (Ed 4) / Committee / ISO/TC 67/SC 4
Edition number / 4 / Vienna agreement / ISO lead
English title / Petroleum and natural gas industries -- Drilling and production equipment -- Wellhead and christmas tree equipment
French title / Industries du pétrole et du gaz naturel -- Équipement de forage et de production -- Équipement pour têtes de puits et arbre de Noël
Start date / 2008-04-10 / End date / 2008-09-10
Opened by ISO/CS on / 2008-04-10 00:00:23 / Closed by ISO/CS on / 2008-09-12 00:04:51
Status / Closed
Voting stage / Enquiry / Version number / 1
Note
Result of voting
P-Members voting: 13 in favour out of 13 = 100 % (requirement >= 66.66%)
(P-Members having abstained are not counted in this vote.)
Member bodies voting: 0 negative votes out of 16 = 0 % (requirement <= 25%)
Approved
Votes by members
Country / Member / Status / Approval / Disapproval / Abstention
Argentina / IRAM / P-Member / X
Austria / ON / X
Belgium / NBN / X
Brazil / ABNT / P-Member / X *
Canada / SCC / P-Member / X
China / SAC / P-Member / X
France / AFNOR / P-Member / X
Germany / DIN / P-Member / X *
Indonesia / BSN / P-Member / X
Italy / UNI / P-Member / X *
Korea, Republic of / KATS / P-Member / X
Luxembourg / ILNAS / X
Netherlands / NEN / P-Member / X *
Norway / SN / P-Member / X
Poland / PKN / P-Member / X
Portugal / IPQ / X
Russian Federation / GOST R / O-Member / X
Spain / AENOR / O-Member / X
United Kingdom / BSI / P-Member / X
USA / ANSI / Secretariat / X *
P-Member TOTALSTotal of P-Members voting: 13 / 13 / 0 / 1
TOTALS / 16 / 0 / 4
(*) A comment file was submitted with this vote
Comments from Voters
Brazil / ABNT / P-Member / Brazil(ABNT).doc
Germany / DIN / P-Member / Germany(DIN).doc
Italy / UNI / P-Member / Italy(UNI).rtf
Netherlands / NEN / P-Member / Netherlands(NEN).doc
USA / ANSI / Secretariat / USA(ANSI).doc
Comments from Commenters
ISO / ISO.doc
Template for comments and secretariat observations / Date: 2008-09-10 / Document: ISO DIS 10423 (4Ed)
1 / 2 / (3) / 4 / 5 / (6) / (7)
MB1
/ Clause No./
Subclause No./
Annex
(e.g. 3.1) / Paragraph/
Figure/Table/Note
(e.g. Table 1) / Type of com-ment2 / Comment (justification for change) by the MB / Proposed change by the MB / Secretariat observations
on each comment submitted
DE / General / te / Before publication all normative references in Clause2 and the rest of the document shall be checked,
a) whether they are up-to-date,
b) whether the references of Clause2 are to be found in the rest of the document and vice versa.
c) whether they are normative and not informative.
US / Entire Document / Other / Replace ISO 10423 Annex J with API Annex Q most recently approved wording on repair and remanufacture. / See attached as a separate copy
US / 2 / te / ISO 18265 is not listed in clause 2, but is referenced in the body of standard / Include ISO 18265 as normative reference
US / 2 / te / ASTM E140 is not listed in clause 2, but is referenced in the body of the standard / Include ASTM E140 as normative reference
US / 2 / te / ASME B1.3 is not listed in clause 2, but is referenced in the body of the standard / Include ASME B1.3 as normative reference.
US / 2 / te / ASME BPV:2004 with 2005 & 2006 addenda, Sec VIII Division 3 is not listed in clause 2, but is referenced in the body of the standard / Include ASME BPV: 2004 with 2005 & 2006 addenda, Sec VIII Division 3 as normative reference.
IT / 2 / ed / ISO 15156 series and NACE MR0175/ISO 15156 series are different identical standards which can be used as dual normative references. / Include NACE MR0175/ISO 15156 series in the list of normative references.
IT / 2 / ed / The API RP 14F title is not correct. / Change to “Recommended practice for design and installation of electrical systems for fixed and floating offshore petroleum facilities for unclassified and class I, division 1 and division 2 locations.”
IT / 2 / ed / ASME B1.1 title is not correct. / Change to “Unified inch screw threads (UN and UNR thread form).”
IT / 2 / te / ASME B1.2 and ASME 1.20.1 are expressed in US customary units only. Combining values from the two systems (US and SI) may result in errors. / Corresponding International (regional, national) standards shall be used for SI units as dual normative references: for example, ISO 262, ISO 7-1, BS 3643, BS 2779, BS 21, etc.
IT / 2 / ed / ASME BPVC-V:2004, ASME BPVC-VIII-1:2004, ASME BPVC-VIII-2:2004, ASME BPVC-IX:2004 and ASTM A703/A703M are already revised standards. / Check 2007 editions.
IT / 2 / te / International (European) standards should be also used as alternative (dual) normative references to ASTM standards. / The following International (European) standards can be analysed as equivalent: EN 10269 to ASTM A193M and ASTM A320M; ISO 6892:1998, ISO 7438:2005 to ASTM A370; EN 10228-3, EN 10228-4 to ASTM A388M.
IT / 2 / ge / Some national standardization bodies (for example in 12 Former Soviet Union countries - CIS) require a translation all normative references during adoption of International standards. There are also difficulties with a national adoption of International standards with non international/regional normative references (without dual normative references).
Thus, normative references should be limited to those that are absolutely required as an integral part of the standard in order to avoid a big amount of work during a national adoption of this standard (for example, to translate 65 normative references in 11 languages during national adoptions of ISO 10423 in CIS) . If necessary, the appropriate requirements should be stated in full in the standard, thereby avoiding the need for the normative reference. Non normative references (without a verbal form “shall”) can be replaced in a bibliography.
If the ISO and US references provide the same technical result for a particular provision, but there is a market need to retain the traditional US reference, then write the provision in accordance with ISO/TC67/N435, Annex I. See also ISO 11960 as an example. / Check all normative references.
** / General / Please verify that the symbols are unique and that each physical quantity is represented by a single symbol, subscripted appropriately (for example, see comment for 4.3.3.2 regarding "S" and comments for G.5.2 )
** / Clause 3 / It would be useful to have a complete symbols list (?included as part of 3.2 or as a separate subclause) in order to verify that the symbols are unique
IT / 3 / 3.1.28 / ed/te / CRA definition- Note: ISO 15156 (MR 0175, clause 2). It is not clear the reference to clause 2. This reference is used in many part of the document. / Please clarify the sentence (MR 0175, clause 2).
IT / 3 / 3.1.89 / ed / The Note is inconsistent with the “proration bean” / Note to be deleted
IT / 3 / 3.1.90 / ed / The Note is relevant to” proration bean” / Note to be moved under 3.1.89
DE / 3 / te / According to ISO/IEC Directives Part2:2004, D.1.5.2,
a definition shall not take the form of, or contain, a requirement.
Check for all definitions.
DE / 3 / te / According to ISO/IEC Directives Part2:2004, D.1.5.3, the form of a definition shall be such that it can replace the term in context. Additional information shall be given only in the form of examples or notes.
Check for all definitions.
DE / 3 / te / According to ISO/IEC Directives Part2:2004, D.3.4, Terms shall in general be presented in their basic grammatical form, i. e. nouns in the singular, verbs in the infinitive.
Check for all definitions.
NL / 3.0 / SUGGEST TO INCLUDE SANDY SERVICE
US / 3 / 3.1.10, 3.1.36, 3.1.45, 3.1.51, 3.1.72, 3.1.99 2nd term, 3.1.112, 3.1.115, 3.1.117 / Te / Term not used in document / Remove definition
US / 3.1.24, 3.1.28, 3.1.37, 3.1.39, 3.1.53, 3.1.56, 3.1.57, 3.1.60, 3.1.65, 3.1.99, 3.1.109, 3.1.118, 3.1.119, 3.1.125, 3.1.130, 3.1.135 / Ed / Second term should not be bolded. / Remove bold from second term
US / 3.1.79 / Ed / Extraneous text / Remove strikethrough text
US / 3.1.89 / Ed / Incorrect NOTE / Remove exisiting NOTE and replace with NOTE from 3.1.90 below it to read:
NOTE: proration is a system of allocating the amount of oil or gas a well or field is allowed to produce within a given period by a regulatory agency.
US / 3.1.90 / Ed / Extraneous text / Remove NOTE.
US / 3.1.108 / Ed / The term "specified material" is not used in the document by itself. Everywhere in the document, it is called manufacturer-specified material. / Change the term to be "manufacturer-specified material" with the same definition.
US / 3.1.56 / Ed / alternating steps of controlled heating and cooling of materials for the purpose of changing physical or mechanical properties
The word “alternating” implies going back and forth between two states. / A specified, timed sequence of heating and cooling…
US / 3.1.26 hub / Ed / protruding rim with an external angled shoulder and a sealing mechanism used to join pressure-containing equipment
Reason: the term “hub” is also used to describe that portion of a flange that extends from the back face of the flange. It is specified for the 6B flanges with the X dimension and for the 6BX flanges with the J1, J2, and J3 dimensions. Tables 36 – 47 abound with the term “hub.” Let’s be more specific with clamp hubs, that’s what they have always been called. / 3.1.62 clamp hub protruding rim with an external angled shoulder and a sealing mechanism used to join pressure-containing equipment
US / 3.1.71 Master valve / Ed / lowermost valve on the vertical bore of the christmas tree
NOTE It is used to completely shut in the well.
Reason: The previous definition ignores the existence of the upper master valve which is the SSV on offshore wells. The note implies that the master valve should be used to shut in a well. However the proper practice is to close first the wing valve, then the upper master, and finally the lower master. The objective is to preserve the integrity of the lower master which is part of the primary containment. / Any valve below the wing of a christmas tree in the vertical run.
NOTE:The lower master valve is the last valve closed to completely shut in a well.
Bean Steels? / Remove the note from 3.1.89. Substitute the note from 3.1.90.
US / 3.1.93 Relevant indication / Ed / The examples are examples of non-relevant indications / This should be clarified by removing the “EXAMPLES” heading and saying “for example” on the end of the previous sentence which describes non-relevant indications.
US / 3.1.95 / Ed / Replace “heat reating” with “heat treating.”
US / 3.1.137 weld groove / Ed / area between two metals to be joined that has been prepared to receive weld-filler metal
Reason: It’s two parts, not necessarily two different metals. / The shape of the mating ends of two parts to be joined by welding
US / 3.1.138 weld joint / Ed / fitting together of components in order to facilitate joining by welding
Reason: the present definition is incorrect. A weld joint isn’t the act of fitting anything. / A system comprising two or more parts prepared for welding and the actual weld or welds joining the parts.
US / 3.1.144 wrought / Ed / Substitute “hot and/or cold working” for “forging”.
Reason: Definition too narrow, not including cold work.
US / 3.1.146 / Ed / Replace “0,2% yield offset strength” with “0,2% offset yield strength.”
Reason: incorrect terminology.
US / 4.1 Performance Requirements - General / Ed / SSVs and USVs (clause 10.19) shall be of the PR2 performance level…
Reason: just makes sense.
US / 4.3.1.2 / Ed / Replace “Hub and outlet end” with “Clamp hub end and outlet”
US / 4.3.1.3 / Ed / Reason: To be more specific in accordance with the definitions. / Replace “hub with clamp hub” in the paragraph that follows and in 4.3.1.3
US / 4.3.3.3 / Ed / Reason: correct the incorrect correction made to the earlier editions. The terminology of “distortion energy theory” is universally used in strength of materials texts, to my knowledge. / Change “Theory of constant energy of distortion” To “Distortion energy theory.”
US / Same Topic / Ed / Reason: The ASME method does address discontinuities and stress concentrations. / Replace the sentence “Rules for the consideration of discontinuities and stress concentrations are beyond the scope of this International Standard.” with “Rules for the consideration of discontinuities and stress concentrations are beyond the scope of this method.”
DE / General / te / According to ISO/IEC Directives Part2:2004, 6.5.1, Notes integrated in the text of a document shall only be used for giving additional information intended to assist the understanding or use of the document. These elements shall not contain requirements or any information considered indispensable for the use of the document.
Check for all notes.
DE / General / te / According to ISO/IEC Directives Part2:2004, 6.4.1.1, Informative annexes give additional information intended to assist the understanding or use of the document. They shall not contain requirements, except as described in 6.4.1.2. According to ISO/IEC Directives Part2:2004, 6.4.1.2, Informative annexes may contain optional requirements. For example, a test method that is optional may contain requirements but there is no need to comply with these requirements to claim compliance with the document.
Check for all informative Annexes.
BR / 4.1 / te / Design assumptions regarding lubrication
(grease - applicable to items 4.1, 4.2, 4.3, 4.7, 10.19.2.1, F.2.2.1 and F.2.3.1)
Actuation performance is greatly affected by friction coefficients, especially on valve side.
If valve is designed to be operational necessarily using lubrication (grease) to reduce wearout or friction, manufacturer shall provide objective evidences that such lubrication is not removed during service life (typical 20 years).
Operator experience on different design validations have shown that preservation of lubrication cannot be assured. In order to obtain a test that is more representative for worst-case service conditions, design validation tests (as annex F and I) should be done with a degreased valve, although initial prototype lubrication should be maintained, to provide initial functional data between validation (prototype) and forthcoming products (FAT on greased valves). / Revise text: “Other requirements…” to:
“Other requirements include load capability, cycles, wear-out and lubrication, and operating force or torque”
BR / 4.2 / te / Design Assumptions:
There are 3 revision claims:
1) Design assumptions regarding lubrication (grease - applicable to items 4.1, 4.2, 4.3, 4.7, 10.19.2.1, F.2.2.1 and F.2.3.1)
2) Design assumptions regarding hydrate or particulate (sand) accumulation inside valve.
3) Design assumptions regarding reliability of verified cycling life for different equipments or applications, compensation cycle degradation.
Actuation performance is greatly affected by friction coefficients, especially on valve side.
If valve is designed to be operational necessarily using lubrication (grease) to reduce wear-out or friction, manufacturer shall provide objective evidences that such lubrication is not removed during service life (typical 20 years).
Operator experience on different design validations have shown that preservation of lubrication cannot be assured. In order to obtain a test that is more representative for worst-case service conditions, design validation tests (as annex F and I) should be done with a degreased valve, although initial prototype lubrication should be maintained, to provide initial functional data between validation (prototype) and forthcoming products (FAT on greased valves).
Regarding fluid with particulates, if valve is lubricated with grease, depending on the amount of filling (see clause 7.4.9.3.3 – “Conduct tests prior to the addition of body-filler grease. Lubrication applied during assembly is acceptable.”) movement restrictions on obturator caused by sand accumulation and increased wear-out (sandpaper effect). In order to avoid or minimize these issues, design shall evaluate these conditions, and appropriate tests shall demonstrate design robustness and endurance to additional wear-out, loads and/or movement restrictions.
Also, flow considerations can be different on gear or ROV operated (typically not operated during high flow conditions) or FSC-actuated valves.
Regarding cycling life of a given equipment (e.g. SSV or USV), the same design can be used with more confidence if PR-2 verified (200 cycles - annex F) and real life actuation is expected to be done a few dozens of operations in say, 20 years of service life. However, if the same valve design is assembled with a FSC actuator and flow assurance (wax / hydrate) demands 1 operation per month, the same design could face more than 200 operations in the same time frame. So, annex F verification should address higher cycling rates than PR-2, in order to provide similar confidence in reliability and endurance requirements.
Other equipments, as swivels and connectors should be capable of more than PR-1 (0 to 3 cycles) but less than PR-2 (200x) and ISO standard should present a minimum requirement, not leaving just as Per Manufacturing Rating (PMR), because manufacturers typically do not provide consistent designed data, expected for operation.
Degradation of operation is affected by cycling, service and operational conditions, lubrication and friction figures and shall be explicitly considered in the design. / Include sub-clause 4.2.4, where final text can be worked by MB workgroup.
4.2.4 – Other (Flow, Fluid and Life-Cycling) ratings
4.2.4.1 – General
Equipment shall be designed to operate under potential flow induced (hot multiphase flow) grease removal, hydrate formation or particulate accumulation inside valve causing movement restrictions and increased wear-out, frictions and loads. Manufacturer shall provide designed endurance capability of the equipment, compatible with expected service and cycling for each designed application.
4.2.4.2 – Design considerations
a)Design shall consider the effects caused by grease removal due to flow conditions as increased frictions and loads. This is more significant for SSV and USV equipments.
b)If required by required by purchaser, manufacturer shall demonstrate and validate by testing and calculations at which reliability figures each equipment is capable to operate during its life time and expected number of actuations.
c)Methods to calculate and compensate eventual performance degradation along service life or number of actuations shall be used during design validation and to aid in the establishment of FAT functional criteria.
US / 4.2.3.1 / Paragraph 2 / te / ISO 15156 limits H2S partial pressure for certain stainless steels and not for carbon steel. So, standard should not allow use of Stainless steels in place of carbon steels only on basis of mechanical properties. / Reword this paragraph as follows: Provided the mechanical properties can be met, corrosion-resistant alloys may be used in place of stainless steels.
US / 4.3.3.1 / Paragraph 3 / ed / Need to clarify ASME BPV referenced in paragraph is an example of a method. / Change the first sentence of the third paragraph to:
In the event … other methods identified by the manufacturer, such as ASME . . . Division 3, shall be used to justify these stresses.
BR / 4.7 / ed / Design Validation
Clarifications regarding SSV and USV normative validation requirements
Reading 10.5, 10.19 and Annex I.1.4 it is understood that SSV and USV shall be PR-2 verified (I.1.4: “The valve to be tested shall be hydrostatically and functionally tested in accordance with 7.4.9 and be PR2-verified”), so validation tests per Annex F PR-2 (F.2.3) are mandatory and shall be performed. However, reading sub-clause 4.7 can induce that Annex F could be optional, being performed only if specified. / Revise text to:
4.7 Design validation
Manufacturers shall document their design validation procedures and the results of performance validation of designs.
Additional validation procedures, including acceptance criteria, are given in Annex F to be used if specified by the manufacturer or purchaser.
Regarding SSVs and USVs , design validation procedures including appropriate acceptance criteria are given in Annexes F and I.
US / 4.2.3.2 / 2 / In order to help insure equipment in Material Classes DD, EE, FF, and HH is used in accordance with the environmental limitations specified in NACE ISO 15156 / NACE MR0175, the full limitations need to be marked on the equipment, not just the H2S limit. Depending on the alloy or alloy family, ISO 15156 / NACE MR0175 may impose limits on the following environmental parameters:
Maximum H2S Partial Pressure
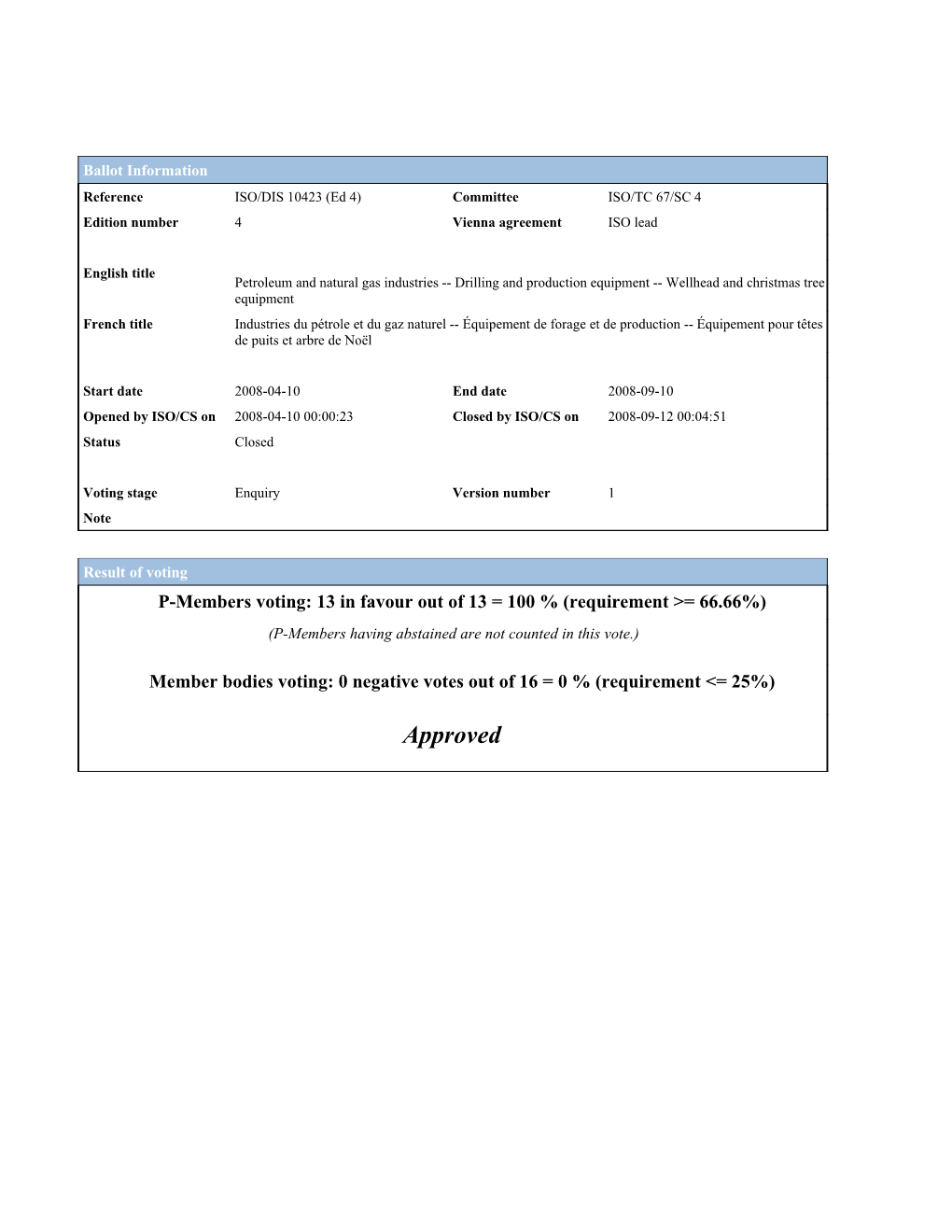