Guide To Plastic
Contents
Why plastic?
Steel / Aluminium / Zinc / Plastic
Raw material cost / £250/Ton / £1,000/Ton / £1,000 /Ton / £1,500/Ton
Strength / 200-500 Mpa / 40-510 Mpa / 160-400Mpa / 60-80 Mpa
Stiffness / 160 Gpa / 75 Gpa / 60 Gpa / 3-4 Gpa
Max. working temperature / 400oC / 180oC / 130oC / 75oC
So Plastic performs abysmally!- why then it the major growth material from the last 50 years! Because it is the most versatile and easily formed material yet devised! Plastic products are produced in one or at most two operations. Plastics require little or no finishing, painting, polishing etc, and particular finishes can be achieved at relatively low cost. Plastics can be coloured during manufacture- no painting etc required. Plastics can be easily printed, decorated or painted. Plastics are corrosion resistant, and generally waterproof. Plastics are lighter than metals, giving deeper sections for a given weight, and hence stronger sections.
There is only one catch:-
To obtain the cost benefits of using plastic products you need the tooling to do it with. This can take the form of an extrusion die, a mould tool, or a former. All of these things are expensive, and take time to make. On www.plaslink.com
Extrusion -
Extrusion is used to make continuous sections only. Parts can however be slit, cut, drilled as secondary operation. eg tubes, gutters, window sections etc. Plastic is squeezed through a two dimensional former or "die", to form a continuous section of material.
Pultrusion -
Similar to extrusion but with much higher Strengths- even used to make road bridges. Glass or other fibres are incorporated into the extrusion and so loadings of up to 60% glass can be achieved with very good fibre alignment. Materials are generally thermosetting type materials such as epoxy.
Rim/Vacuum Casting -
Low volume detailed parts, also used as prototyping system for injection moulding. Chemically curing resins are injected at very low pressures,or drawn into a mould under a vacuum. Long cure times mean that this is an expensive production process.
Injection Moulding -
Volume production system - estimated 80% -90 % of all plastic parts made by this process. Limitation of high tooling cost for most applications. Parts are formed by injecting soft or liquid material into a complete mould under very high pressures. Tooling cost can be reduced by using aluminum or modular tooling systems.
Blow Moulding -
Used to make hollow components, bottles, oil drums, children's furniture etc. Limited choice of materials. Parts are formed by inflating a "bubble" of plastic inside a hollow mould, which gives the finished shape to the product. Variations on process include injection blow moulding, stretch blow moulding, blow moulding using performs.
Rotational Moulding -
Used to make large items, e.g. domestic oil tanks, large bins etc. Items can be hollow, but also used for other products- but generally for parts that form part or all of a shell. Parts are formed by rotating a hollow tool with a charge of powdered plastic inside. The tool is heated, and then cooled, so the plastic fuses to the inside of the tool, to form a shell.
Fibre Reinforced Plastics -
Used where higher strengths and stiffnesses are required than available from other processes, eg golf clubs, vehicle seats. Generally parts are made by various lay up processes and resin is then added and cured by chemical or heat action. Note some Fibre reinforced materials can be injection moulded.
Vacuum Forming -
Used to make large area parts such as trays covers etc. Tooling much cheaper than injection moulding, but three dimensional ribs, bosses etc cannot be formed. Limited choice of materials. Parts are formed by heating a sheet of plastic over a one sided mould or former, until it is soft but not liquid, and then using a vacuum or pressure to suck or push the sheet onto the mould, then allowing it to cool.
Thermoforming -
Similar process to Vacuum forming, but thermoforming refers to thin walled components, such as are used in packaging and display items.
Guide to Plastic
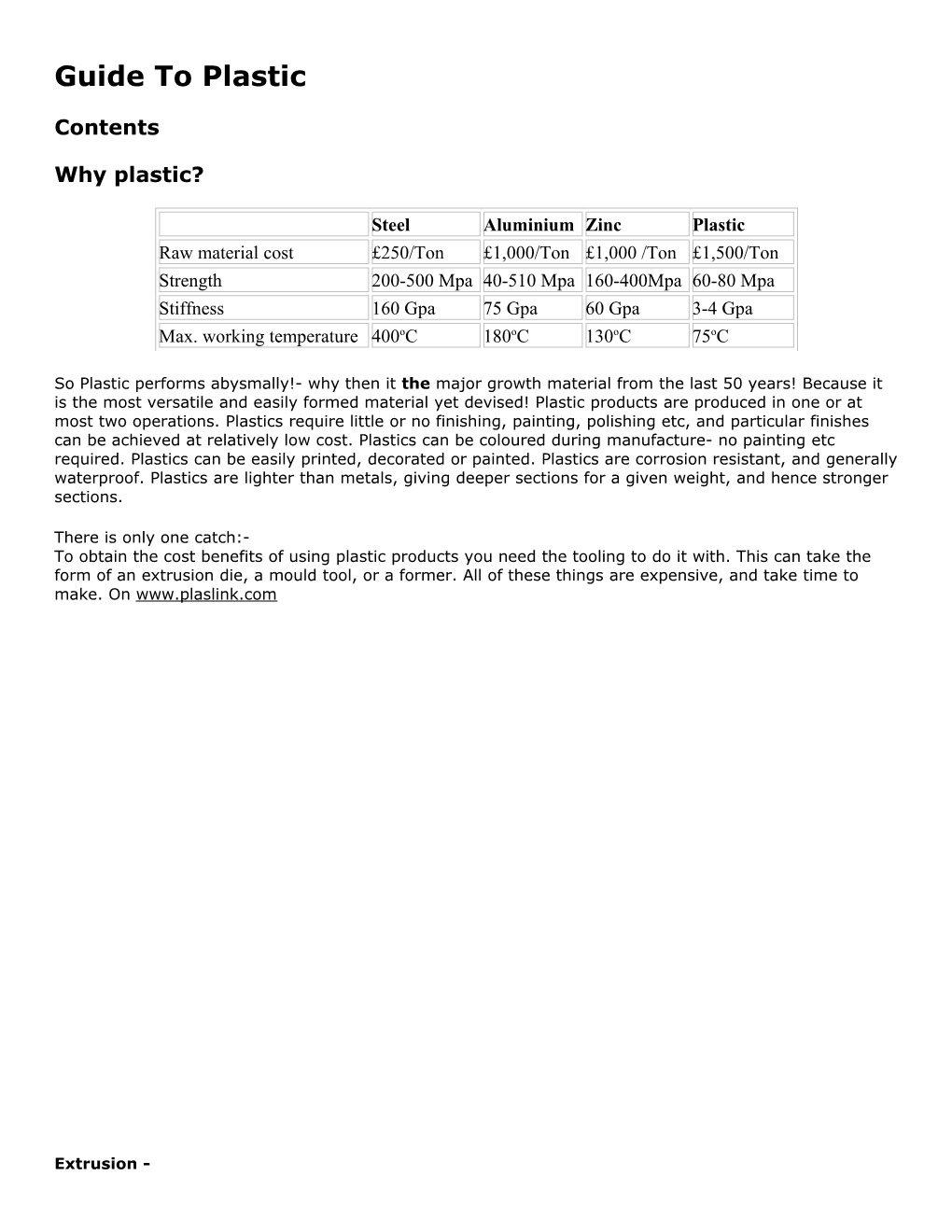