Strategic human resource management of Japanese multinationals - A case study of Japanese multinational companies in the UK
Dipak R. Basu,Victoria Miroshnik.The Journal of Management Development.Bradford:1999.Vol.18,Iss.9;pg.714
» / Jump to full text
Subjects: / Studies,Human resource management,Management development,Multinational corporations
Classification Codes / 9130Experimental/theoretical,6200Training & development,9175Western Europe,9179Asia & the Pacific,9510Multinational corporations
Locations: / United Kingdom,UK,Japan
Author(s): / Dipak R. Basu,Victoria Miroshnik
Article types: / Feature
Publication title: / The Journal of Management Development.Bradford:1999.Vol.18,Iss.9;pg.714
Source Type: / Periodical
ISSN/ISBN: / 02621711
ProQuest document ID: / 116353684
Text Word Count / 5737
Article URL: / http://gateway.proquest.com/openurl?ctx_ver=z39.88-2003&res_id=xri:pqd&rft_val_fmt=ori:fmt:kev:mtx:journal&genre=article&rft_id=xri:pqd:did=000000116353684&svc_dat=xri:pqil:fmt=text&req_dat=xri:pqil:pq_clntid=31317
More Like This»Show Options for finding similar articles
Abstract (Article Summary)
This study analyses the human resources management system in Japanese automobile companies, Toyota and Nissan, in their overseas production plants in the UK and analyses differences between their original human resources management system in Japan and in their foreign operations. It found that these companies, as far as their internal operations are concerned, have tried to implement their original practices in spite of cultural differences. However, in the case of production management system they are not completely successful because of organisational differences in their foreign locations. The paper analyzes the effects of these novel practices on the industrial scene in the UK in general.
Full Text(5737 words)
Copyright MCB UP Limited (MCB) 1999
Dipak R. Basu: Nagasaki University, Japan
Victoria Miroshnik: Nagasaki University, Japan
Japanese manufacturing organisations have made a lot of inroads in overseas production bases. The successes of their enterprises have raised interests on the system of production and organisation peculiar to the Japanese business firms (Wickens, 1987; Suzaki, 1987). Particularly that is true about the automobile production sector where non-Japanese firms are adopting Japanese methods of management in a number of countries in order to compete effectively against Japanese firms (Womack et al., 1990; Monden, 1983; Hayes, 1981; Imai, 1986). Spread of this enthusiasm is basically due to the foreign production bases of some leading Japanese automobile companies. In order to understand the strategic management issues regarding Japanese overseas affiliates we discuss here the essential characteristics of the Japanese system of management (Hayes, 1981; Shingo, 1981, 1985).
Japanese system of management is a complete philosophy of organisation which can affect every part of the enterprise. There are three basic ingredients: lean production system, total quality management and human resources managements (Ohno, 1978; Nohara, 1985). These three ingredients are interlinked in order to produce total effect on the management of Japanese enterprises. Because Japanese overseas affiliates are part of the family of the parent company, their strategic managements are part of the management strategy of the parent company (Shimada, 1993; Abo, 1994; Morita, 1992).
The basic idea of the lean production system is described in Table I. The fundamental principles are described at the bottom of Table I. At all levels the fundamental idea is "humanware" (Shimada, 1993) which is described in Figure 1. "Humanware" is defined as the integration and interdependence of machinery and human relations and a concept to differentiate between different types of production systems.
The purpose of this paper is to analyse management styles in Japanese automobile companies in their foreign locations and to examine how far they maintain their original management styles in foreign locations. A number of studies have indicated that management styles depend on the types of organisations and their strategic ambitions (Blyton and Turnbull, 1994; Purcell, 1987; Edwards, 1995; Purcell and Ahlstrand, 1994; Goffee and Scase, 1995). In the existing studies of Japanese multinational companies no clear pictures emerge. In a number of cases, particularly in USA cultural factors dominate over the global organisational plans (Florida and Kenney, 1991). Similar experiences are observed in the case of operations of American overseas companies (Kujawa,1979; Hofstede,1985; Negandhi et al., 1985; Hofstede, 1993). We have analysed two Japanese multinational companies, Nissan and Toyota, in their British operations with particular reference to their human resources management styles.
The method of analysis is basically interviews with the workers and managers of these two companies, Nissan and Toyota, in both Britain and Japan. We have described in detail questionnaires we have used and the answers we have received. We have visited the Sunderland plant of Nissan and the Barnaston plant of Toyota. In Japan we have visited the Sizuoka plant of Nissan and the Nagoya plant of Toyota. We have interviewed 250 workers chosen randomly in each plant. For questions regarding management strategies, we have interviewed vice-presidents, plant managers and directors of these companies in the UK.
Japanese management system: an overview
We discuss below some of the important features of the Japanese management system.
Continuous improvement
The constant strive for perfection (Kaizen in Japanese) is the overriding concept behind good management, in which the production system is being constantly improved; perfection is the only goal. Involving everyone in the work of improvement is often accomplished through quality circles. These are activities where operators gather in groups to come up with suggestions on possible improvements. There are schemes for implementing suggestions, rewarding employees and feeding back information on the status of the suggestions.
Zero defects
In order to attain high productivity it is essential that all parts and products are fault-free from the very beginning. The goal is to work with products that are fault-free through the continuous improvements of the manufacturing system. Thus zero defects denote how a lean company works in order to attain quality. In a lean production system it is important to move towards a higher degree of process control. Each process is controlled through knowledge gathered about the parameters of the process. Thus instead of controlling the parts produced the process is kept under control. The idea is to prevent defects from occurring, through discovering errors that can lead to defects. Lean production system uses "autonomous defect control" which is an inexpensive means of conducting inspection of all units to ensure zero defects. Quality assurance is the responsibility of everyone. Identification of defective parts is the responsibility of workers, who are allowed to stop the production line in the event that defective parts are found. Responsibility for adjusting the defective parts is delegated to workers. As a consequence the number of personnel working in the quality control department can be reduced; the size of the adjustment and repair areas can be reduced too.
Manufacturing tasks are organised into teams. This makes the workers more aware of the need to manufacture only fault-free parts. An important reason for the improved awareness was that the physical contact between manufacturing stages allowed for better communication. Largely through the use of teams, workers found it beneficial to have the responsibility for correction resting with that part of the process where the error has been committed. Through the use of statistical process control, with tests after each process, the company can get better control over their production processes.
Just-in-time
Accomplishing fault-free parts is a prerequisite to achieving just-in-time deliveries. The principle of just-in-time means each process should be provided with the right part, in the right quantity at exactly the right point of time. The ultimate goal is that every process should be provided with one part at a time, exactly when that part is needed. It is possible to have different levels of just-in-time. First, there is the case when parts are moved between different processes in lots. Second, parts are differentiated according to product variants. Third, there is sequential just-in-time. Here parts arrive with reference to the individual products on the line. For example, car seats may arrive at the assembly line in the exact order in which they are needed. In general, the higher the level of just-in-time a company can master the better. However, sequential just-in-time is not always needed. It will vary depending on the nature of the products. When the products are standardized and relatively inexpensive it may not be too important to achieve the highest level of just-in-time.
Pull instead of push
Scheduling of materials is closely related to the principle of just-in-time. It is useful to look at the relationship between forward scheduling and backward request. Before starting to implement lean production in a company final assembly is made to customer order. In all other stages of the manufacturing process productions are according to a forecast. Gradually the number of manufacturing stages producing according to customer order has to be extended. Thus somewhere in the material flow is a point where pull meets push. Behind this point, backward requests are used. Ahead of the point there is forward scheduling. This may create difficulties in stock-outs or too large stocks at this pull-push point. This can be due to the difficulties in making correct forecasts (Karlsson and Ahlstrom, 1996).
Multifunctional teams
The most important feature of the organisational set-up of the lean production system is the extensive use of multifunctional teams, which are groups of workers able to perform many different works. The teams are organised along a cell-based production flow system. Owing to the rotation of the tasks in a team, the increased flexibility reduces the vulnerability of the production system. The number of job-classifications also declines. Workers have received training to perform a number of different tasks, such as statistical process control, quality instruments, computers, set-up performances, maintenance etc. They also have to be trained in a number of functional areas such as materials management, purchasing, maintenance and quality controls. The company has to rotate the workers among tasks frequently.
Decentralised responsibilities
In the lean production system responsibilities are decentralised. There is no supervisory level in the hierarchy. The multifunctional team is expected to perform supervisory tasks. This is done through the rotations of team leadership among workers. As a result the number of hierarchical levels in the organisation can be reduced. The number of functional areas that are the responsibility of the teams increases. People who are not required as a result of the reductions of requirements for indirect controls normally move to other areas because in the Japanese system the company has no lay-off policy (Kumazawa and Yamada, 1989).
Vertical information system
In a multifunctional set-up it is vital to provide information in time and continuously in the production flow. Information can be of two types:
(1) Strategic information about the overall performances and plans of the company.
(2) Operational information about performances of the teams, quality productivity, lead times and other factors in the production process.
Operational information is more frequent than strategic information about market plans, production plans, process development plans and financial performances.
Limits to lean
However, lean production system is not the only alternative to the traditional production system. There are:
(1) German style quality production model based on a highly skilled work consensus;
(2) systemic rationality model, which are common in the information technology firms; and
(3) the Swedish model of Volvo motor company, reflective production system, in which production teams have direct contact with the customers (Cusumano, 1994; Redher, 1994; Sasaki, 1994; Sandberg, 1995; Nomura, 1993; Altmann, 1995; Jonsson, 1995).
Strategic managements of Japanese multinational companies overseas
Strategic management of a multinational company involves evaluations of its own domestic competitiveness and utilises these experiences in a global setting. At the same time the company has to decide the configurations of its operations across the world, i.e. where to locate which facility. Some detail analysis of two Japanese multinationals, Nissan and Toyota, and examinations of basic characteristics of their operations and their style of management are presented below.
Nissan
Nissan Motor Manufacturing (UK) Ltd was established in 1984 as a part of the Nissan Japan's global investment strategies. The production started in 1986. Nissan announced, in that year, plans to accelerate the UK manufacturing programme by increasing local content to 60 per cent by 1988 and 80 per cent by 1991 with a plan to produce 100,000 units. By 1994 Nissan from its UK production base has exported cars to 34 different world markets. By 1995 Nissan's total investment reached Pounds 1.25 billion in the UK and the plant in the UK has produced one million cars and one million engines (Company Report, Nissan, 1998).
Employment in the UK plant has gone up from 470 in 1986 to 4,038 in 1995. Total production in 1995 reached 215,346. Out of that 161,215 were for export to other countries. Thus Nissan has successfully used the UK as its export base. At the same time it has created a network of suppliers throughout Europe.
The philosophy of the company in the UK and the management system
According to the company profile "Nissan's Sunderland (UK) plant aims to build profitably the highest quality car sold in Europe to achieve the maximum possible customer satisfaction and thus ensure the prosperity of the company and its staff". Company's management style reflects that.
Organisational layout of production management system
Nissan plant in Sunderland, UK includes a car and component manufacturing facility, an engine machining and assembly plant, a foundry, a plastics injection and blow-moulding plant and a service parts operation all on one site. Environmental considerations are high in the list of priorities in the production system. The use of water based paints, increased volume of recycling activities and the provision of a good operator environment are some of the elements. "Just-in-time" production systems are applied throughout internally. Nissan does not build a large buffer stock of doors, bonnets, and boot lids, the total amount of stock in process time in the body assembly plant is less than one hour. Production flow chart (Figure 2) reflects the optimum design set-up according to the internal "kanban" system. In the "kanban" system each department of the production process should be located in a logical style so as to provide a continuous flow of materials as demanded by the production process. The idea is not to have any inventory in each department but to demand when required. The production management system and plant design must ensure that these demands can be met immediately. Lay-out design of the plant is crucially important as most processes are automated , run by robotics. Optimum lay-out of plants ensures that no robotic system would stay idle or run into each other. Each department puts up a notice outside if they need some parts or components. This "notice" is then photographed by overhead cameras and the information gets transmitted to the central material management centre who transmits this to the suppliers and to the parts manufacturers. In Japan, parts manufacturers are located within a radius of five miles from the main plant, thus external "kanban" is feasible. In the UK, external "kanban" is not possible, because parts manufacturers are located in different parts of the UK and far from the main plant.
Strategic Human Resource Management Of Japanese Multinationals - A Case Study Of Japanese Multinational Companies In The UK
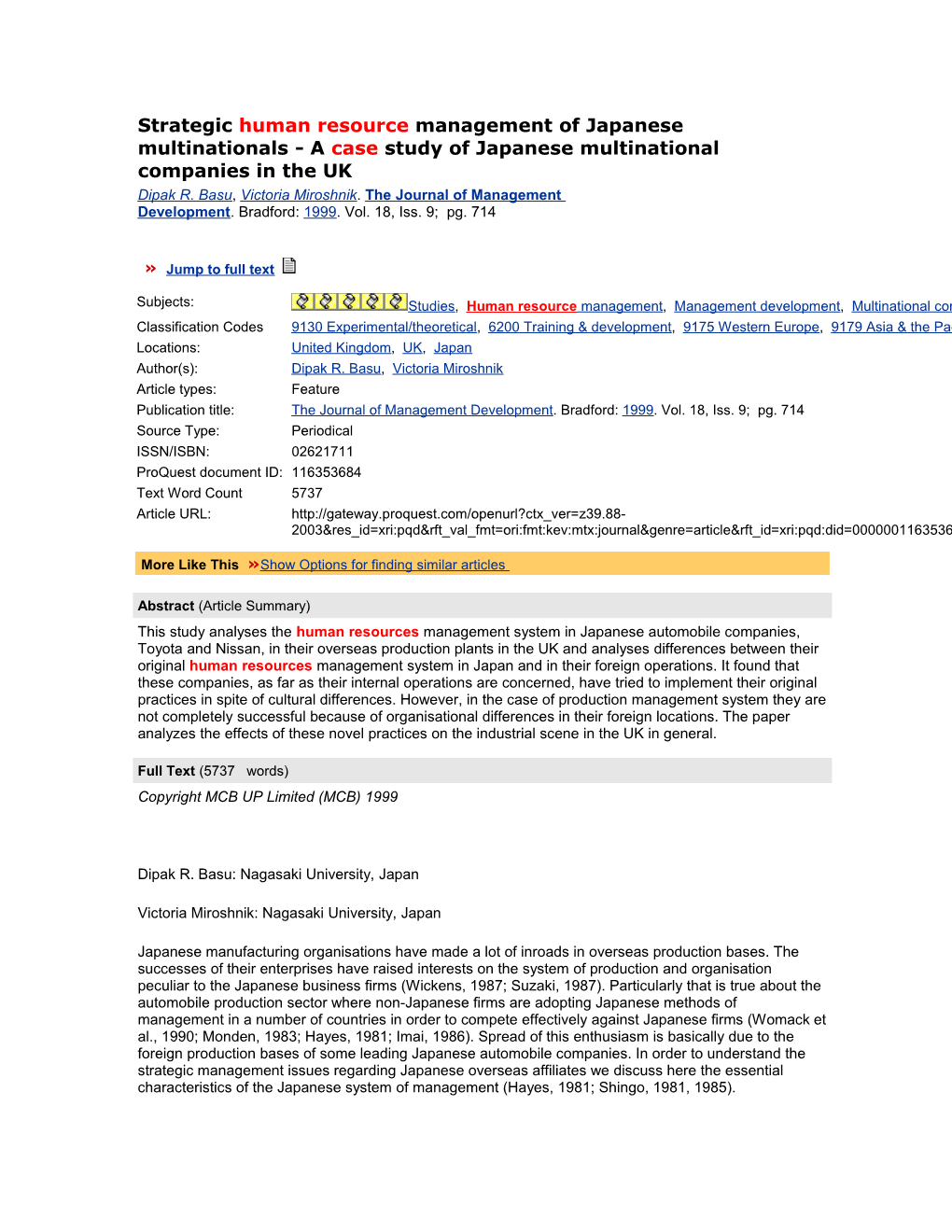