Domestic Construction Timber Framing Completion Checklist
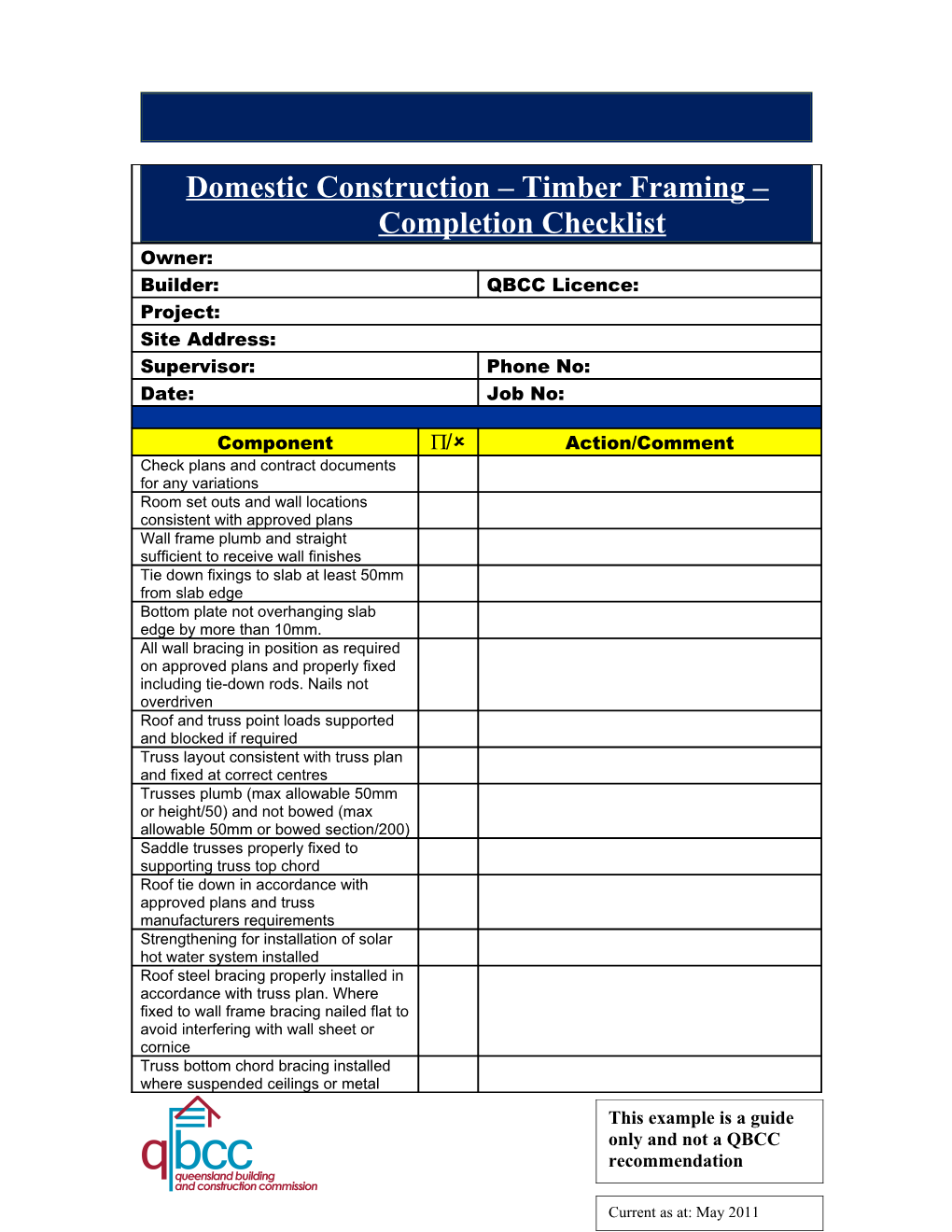
Domestic Construction – Timber Framing – Completion Checklist /
Owner: /
Builder: / QBCC Licence: /
Project: /
Site Address: /
Supervisor: / Phone No: /
Date: / Job No: /
Component / P/û / Action/Comment /
Check plans and contract documents for any variations
Room set outs and wall locations consistent with approved plans
Wall frame plumb and straight sufficient to receive wall finishes
Tie down fixings to slab at least 50mm from slab edge
Bottom plate not overhanging slab edge by more than 10mm.
All wall bracing in position as required on approved plans and properly fixed including tie-down rods. Nails not overdriven
Roof and truss point loads supported and blocked if required
Truss layout consistent with truss plan and fixed at correct centres
Trusses plumb (max allowable 50mm or height/50) and not bowed (max allowable 50mm or bowed section/200)
Saddle trusses properly fixed to supporting truss top chord
Roof tie down in accordance with approved plans and truss manufacturers requirements
Strengthening for installation of solar hot water system installed
Roof steel bracing properly installed in accordance with truss plan. Where fixed to wall frame bracing nailed flat to avoid interfering with wall sheet or cornice
Truss bottom chord bracing installed where suspended ceilings or metal furring channel ceiling battens used.
Binders installed
Transfer noggings installed connecting bracing walls to trussed roof frame
Non load bearing walls set down a minimum of ceiling batten depth + 10mm from the level of external load bearing walls.
Non load bearing walls connected to trusses with slotted wall brackets where required.
Entry bulkheads straight and level
Ceilings nogged for plaster sheet joins and at change of direction
Internal door opening sizes consistent with plans
Bottom plate removed from all internal doorways
Internal bulkheads installed plumb and straight
Plumbing duct and vent pipe framing plumb and straight
Lintel sizes as shown on approved plan
Windows fixed in accordance with window manufacturers requirements or Aust Window Assoc. recommendations
Windows plumb and level
Bath properly framed up and supported with appropriate clearance for tiles and sheeting
Nogging installed for WC cistern and toilet roll holder
Nogging installed for ensuite cistern and toilet roll holder
Nogging installed for bathroom towel rails
Nogging installed for ensuite towel rail
Noggings installed for panel lift door
Noggings installed for clothes dryer
Other noggings required and installed
Manhole correctly positioned & framed.
Fascia fixed and aligned properly
Fascia properly aligned for external cladding or brickwork where there is no eaves overhang
Trimmers and battens installed to eaves to properly fix eaves lining
Temporary bracing removed
Windows checked to ensure they are not damaged
House swept and clear of debris
Site clear of rubbish
Frame inspection passed
Sub-Contractor: / QBCC Licence: